BFLEX for flexibles
The BFLEX program system is a special purpose FEM tool developed for analysis of flexible pipes, umbilicals and power cables during load-out, installation and under in-service load conditions. As a special purpose tool, it is much more efficient than other more general purpose tools in terms of analysis time. The modelling approach is also tailored towards beam/pipe objects and helical components, simplifying the modeling effort.
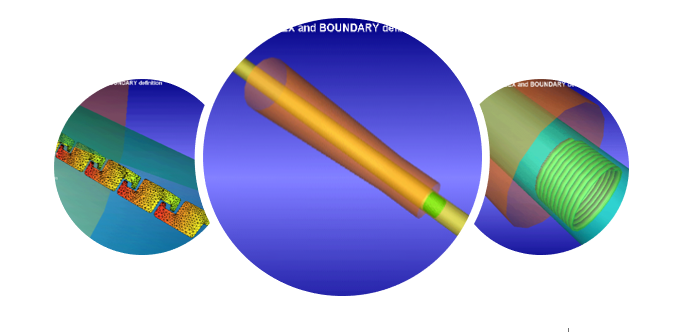
Key functionality
-
Layer by layer definition of flexibles pipes, similar to pipe data sheets
-
Elasto-plastic material properties for fatigue assessment of metallic components in the flexible pipe
-
Prediction of global properties EA, EI and GJ
-
Stress analysis and fatigue assessment of tensile and pressure armor wire
-
Full FE modelling of flexibles, very efficient in computing time compared to general purpose FE software
-
Load conditions as in service, accumulated damage on all nodes for all global sea states
-
Moment curvature relation validated by full scale measurements. Stresses validated by full scale testing using Fiber Bragg Grating technique embedded in tensile armor wires
-
Both bonded and non-bonded flexibles, umbilicals and power cables
-
Stress concentration close to end fitting or due to high curvature gradients
-
Lateral buckling of armour wires under combined compressive and cyclic bending loads
-
Modelling the effect of broken armour wires
-
Different loading scenarios relevant for production, installation and operation, such as
-
Bend stiffener or bellmouth at hang-off
-
Spooling operations during load out
-
Bending over roller supports
-
Key results
-
Strain or stress of functional components
-
Individual stress on components, including friction stress
-
-
Non-linear relation of curvature and bending moment
-
Contact pressure due to axisymmetric load
-
Ovalization of carcass layer
-
Fatigue damage on all metallic components in a flexible pipe, when using the classic BFLEX analysis model
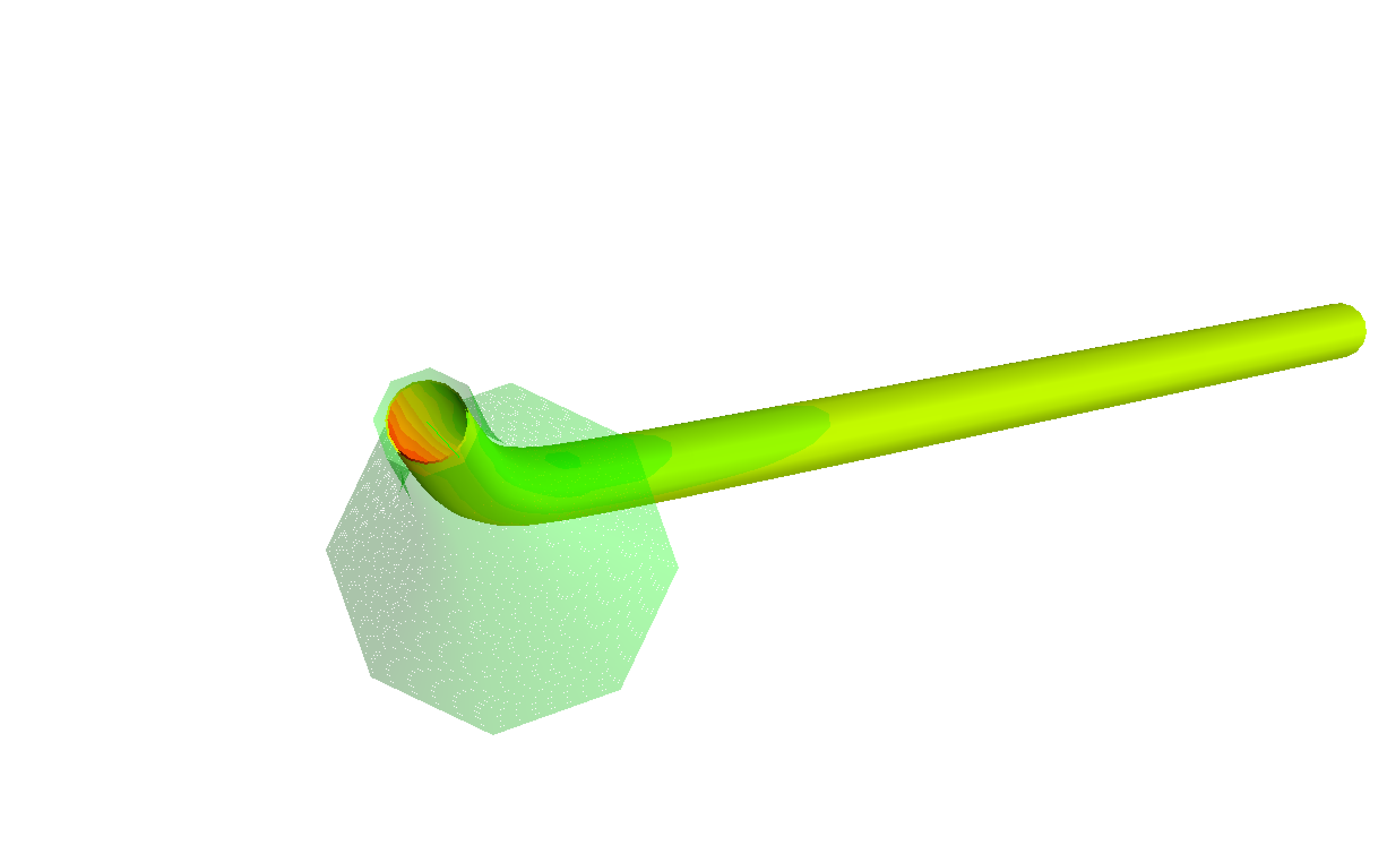
History
The BFLEX development started in the early 90s, and the first generation of BFLEX was focused towards obtaining the global properties of non bonded flexible pipes, as well as the fatigue life of the tensile armour wires. The target load conditions were for the North Sea with fairly constant tension levels corresponding to water depths of a few hundred meters. The effort started based on the PhD work by Svein Sævik, and has since then been further developed in a continous process supported by the oil industry through several industry and joint industry projects.
The original modelling approach included both the moment-curvature and the individual helix sandwich beam model approach. In both cases, the axisymmetric stresses and layer contact pressures are found by applying the CAFLEX model which was developed as a cooperation between SINTEF and IFP. The caflex model assumes concentric layers and Lagrange multipliers to resolve layer contact pressures.
With increasing depths and pressure levels, the need for detailed stress results on the pressure spirals became more important, as a basis for fatigue life calculations. This lead to the development of the PFLEX, BOUNDARY and LIFETIME modules that could extend the level of detail to include stresses and strains in these components. This was developed through a sub-modelling concept, selecting a hot-spot along the riser. A limited number of pressure spirals were included at this location, to be studied in detail capturing the longitudinal and transverse bending moment. In addition a boundary procedure are able to capture stress concentrations at for example corners as well as contact stresses relevant for fretting fatigue. The modules operates seamlessly with BFLEX.
A major development effort to increase the flexibility was undertaken around 2010, which resulted in the new BFLEX2010 framework. This replaced the original BLEX. From that time on, access to the old format required by the PFLEX, BOUNDARY and LIFETIME modules must be established through a post processing step using the BFLEX2010POST postprocessor.
With the new develpment, several options for helical layers were introduced, applying detaled single helix elements or helix layer models. Bi-derectional slip and lateral contact can now be accounted for. The effect of tension variation on the stick-slip transition of the helices during the bending process can be captured. The new functionality enables a wide range of specialist analysis such as lateral buckling of armour wires under compression, broken or missing single wires, spooling operations etc.
From early 2020s, the modelling capabilities of USAP were merged into BLFEX2010. This includes modelling of long pitch length tubular components with limited interaction between helices.
The most recent and on-going developments are mainly related to proper modelling and analysis of power cables.
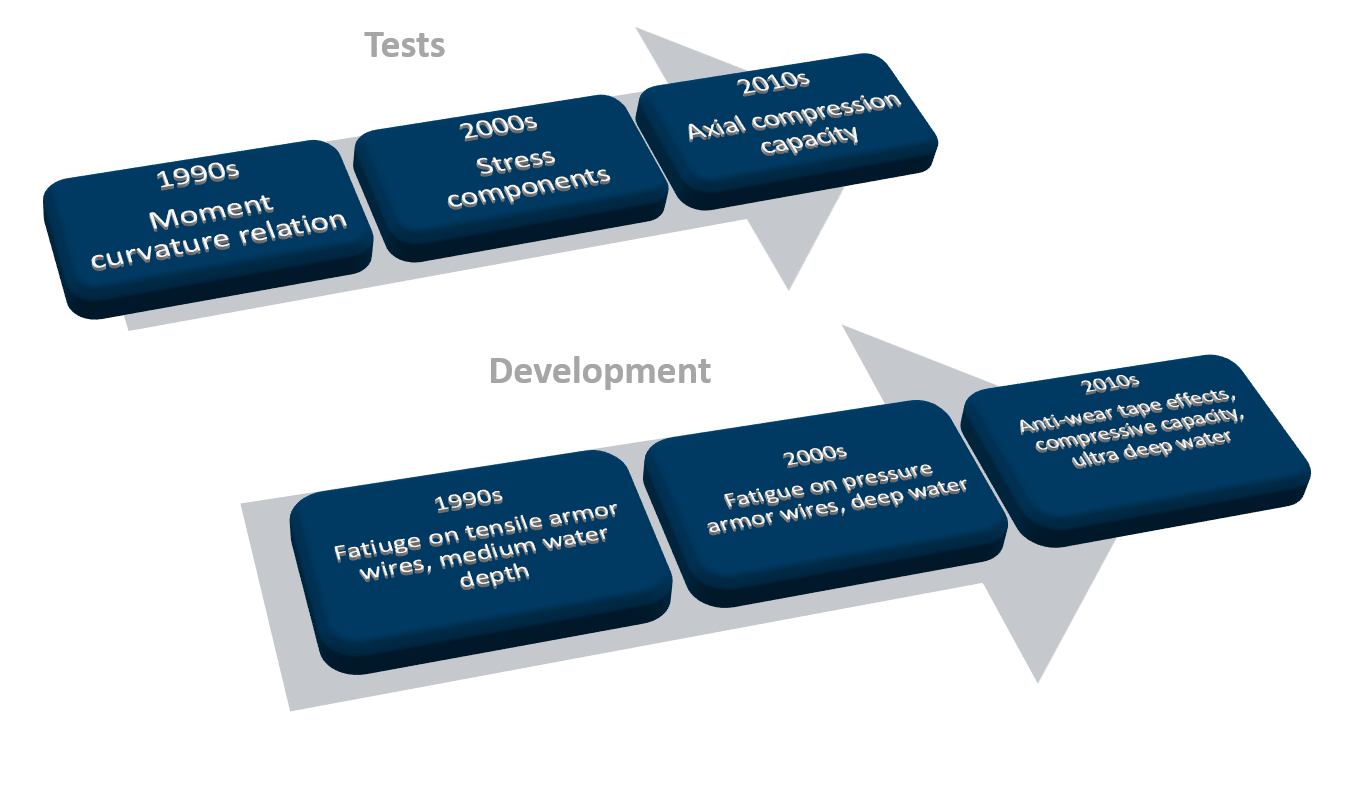
Modules
The input to BFLEX and its different modules are based on text files, and can hence easily be batch processed by scripting and parameter substitution.
Main modules
-
BFLEX2010
Requires a text based input file. Stores analysis results to a binary database. The results can be grapically displayed and/or post processed to ASCII tables. -
BFLEX2010POST
Requires a text based input file. Is used to extract results from the binary result file to ASCII tables. It is also used for translating the result database into the old BLFEX format for further processing by the BOUNDARY, PFLEX, LIFETIME modules. These modules are only relevant for classic PIPE52/HSHEAR352 pipe models. -
DYNPOSTB
Requires a text based input file. Is used to extract time series results at selected model points from the binary result file to ASCII tables. -
BOUNDARY
Requires a text based input file. Operates on a binary database from post processing with BFLEX2010POST. This database is further populated with results from BOUNDARY -
PFLEX
Requires a text based input file. Operates on a binary database from post processing with BFLEX2010POST. This database is further populated with results from PFLEX -
LIFETIME
Requires a text based input file. Operates on a binary database from post processing with BFLEX2010POST, and that PFLEX and BOUNDARY have supplemented with stress results for the pressure spiral.
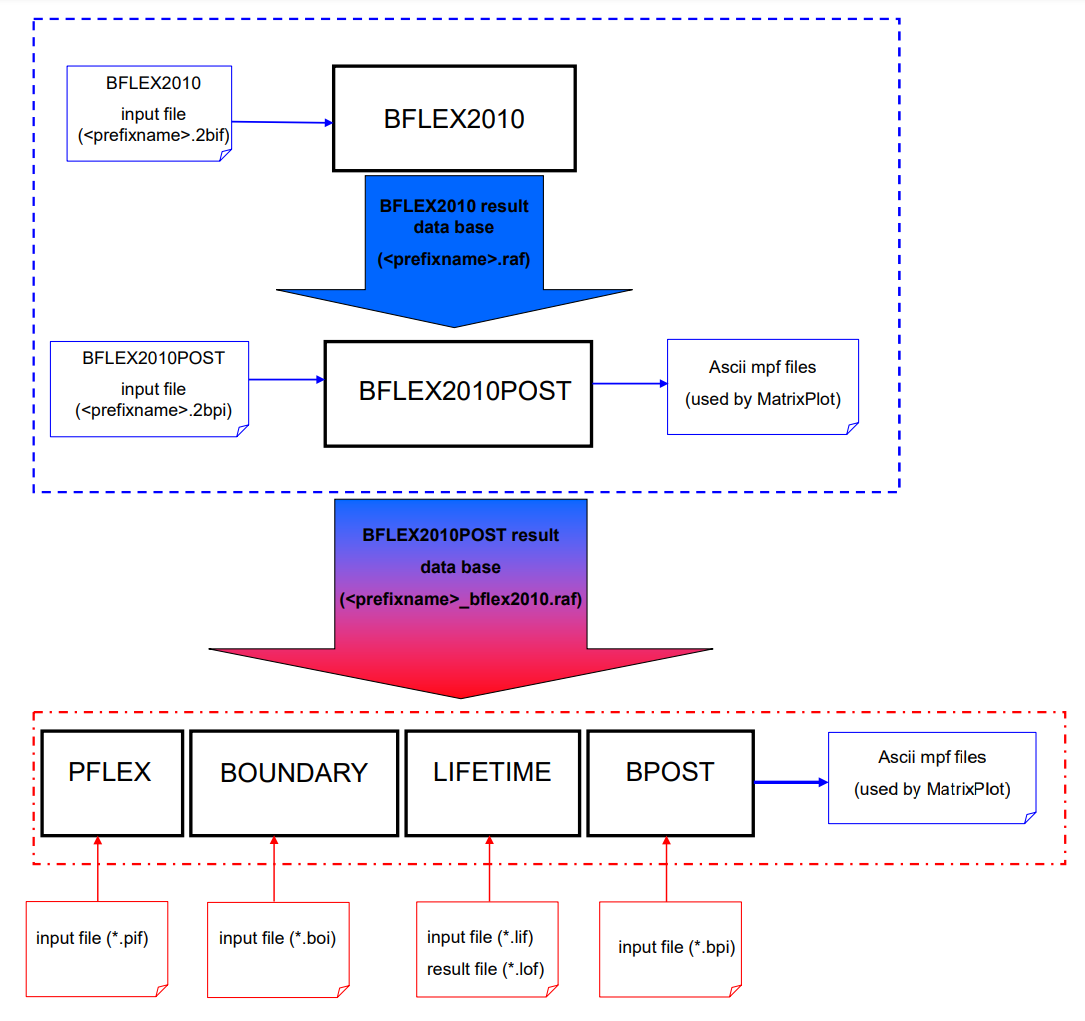
Utility tools
-
Xpost
Operates on the binary database from the analysis, displays the FEM element model and the all the analysis results such as strains, stresses etc.
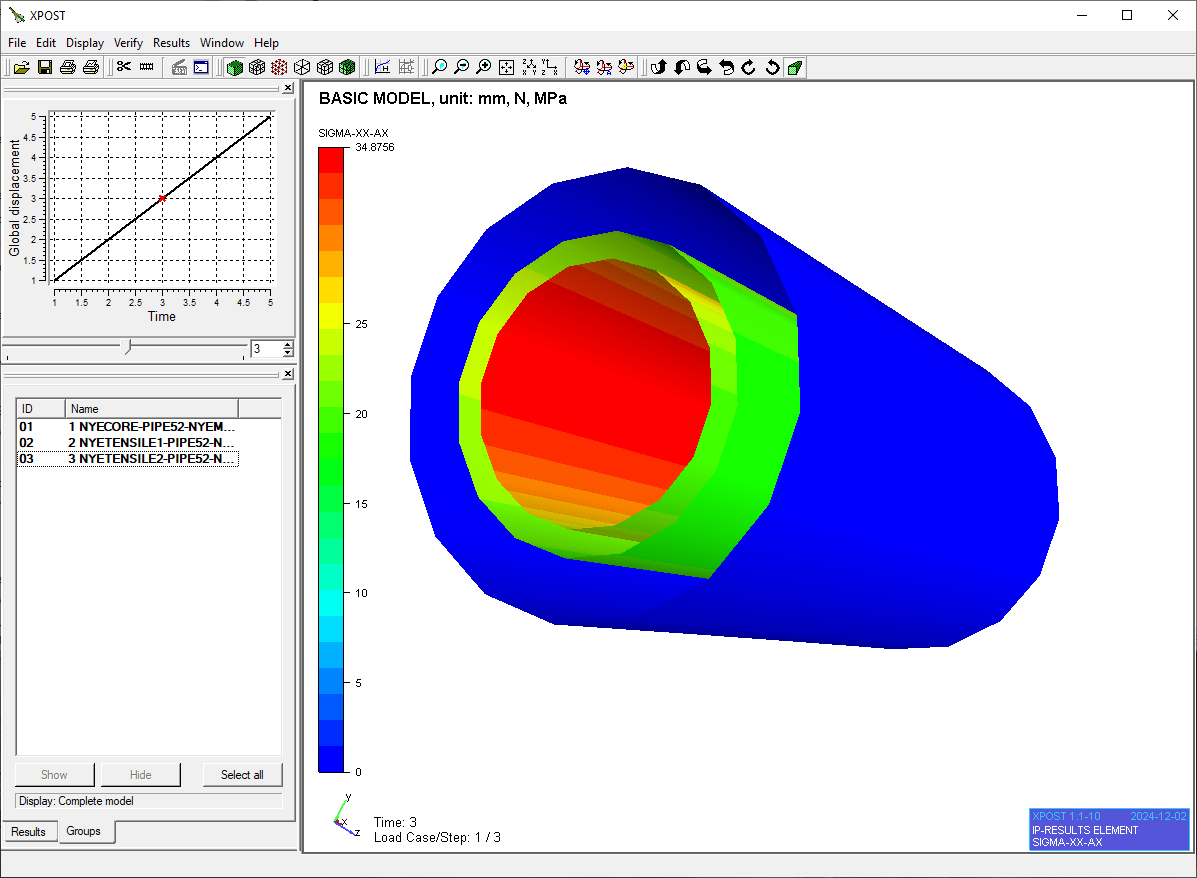
-
Matrix Plot
Plotting tool for the ASCII tables generated by BFLEX2010POST.
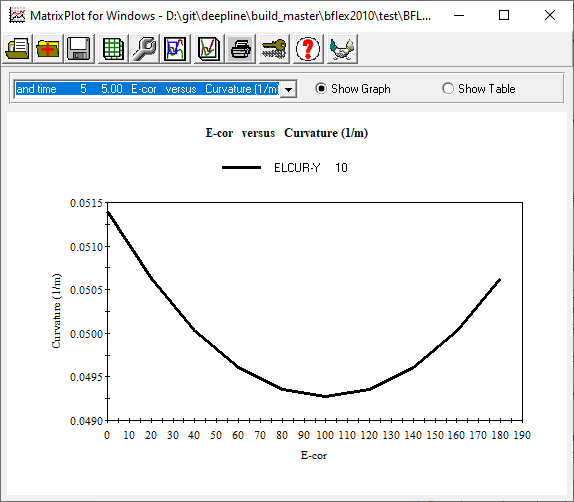
-
Flex Edit
Text editor with help text and easy launch of the modules.
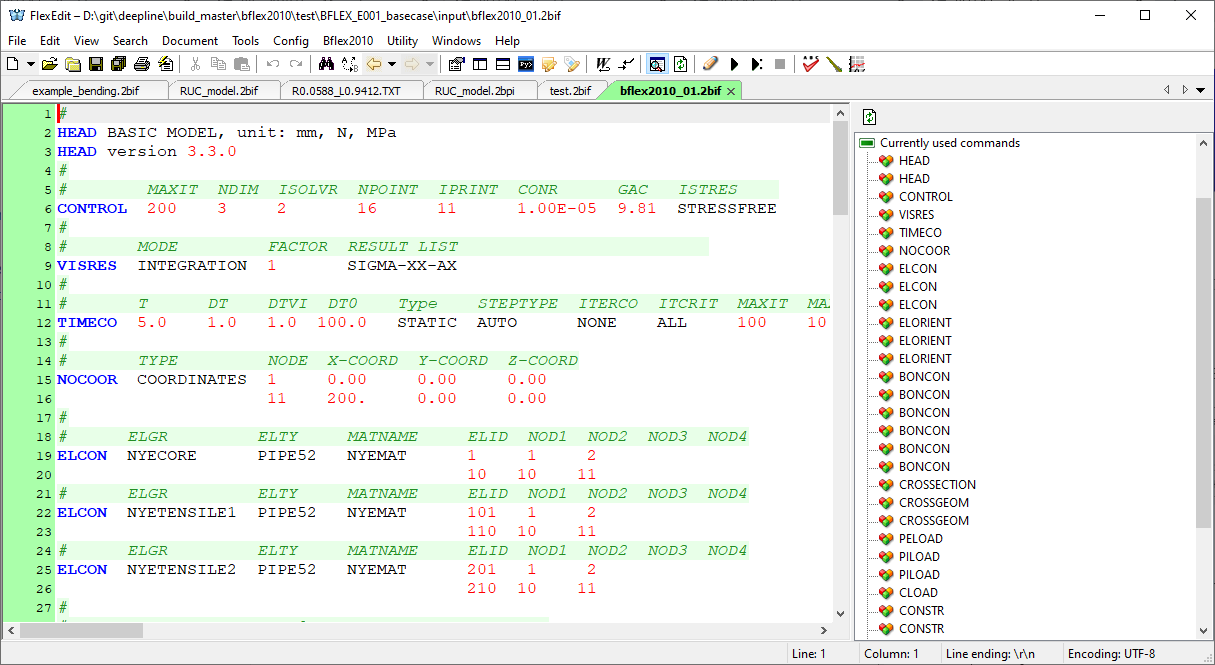
License Options
There are two options for access to the BFLEX software package;
-
Buy a perpetual right to use. With this option you will receive user support and suftare updates for a period of one year after purchase. After the initial year, you will still have right to continue using the BFLEX version that you have accquired. Continued support and updates to the software can be obtained for an annual fee.
-
Rent the software for a limited period, which provides access to the software and user support during the relevant period. Standard rental periods are 6 months or 1 year.
Note that new users are strongly recomended to also purchase a introdutionary course on how to use BFLEX.